Reverse Logistics
Enhance your process for handling returns, warranties, and recalls.
A Vital Element of Logistics
Reverse logistics can be tricky for numerous reasons, but it is a vital element of any logistical endeavor. It is an issue that affects numerous departments, where control is less apparent, and accounting can be more difficult and confusing.
Other challenges of reverse logistics can include:
- The shipping process is not transparent.
- The customer is not equipped to ship.
- Price negotiations with the carrier are ambiguous.
- Product quality is unknown.
- Product packaging is missing or unacceptable for shipping.
- Disposition is not clear.
- Correct routing of product is variable.
- Cost determinations are complex (freight, packaging, disposition).
- Inventory management is not consistent.
- Product lifecycle is less manageable.
Challenges notwithstanding, in today’s world it is important to be prepared in case of a recall or similar event, which require having reverse logistics in place. W.I.S. Logistics handles your logistics issues and turns them into customer satisfaction opportunities and sources of revenue.

Why Choose Us
- Automate and standardize the returns process across the entire enterprise
- Reduce the overall level of returns
- Decrease costs for repair and replacement units
- Shorten replacement turnaround times
- Receive feedback on O.E.M. quality
- Recover assets
- Gain financial R.O.I. for both freight and product
- Offer first-level customer support
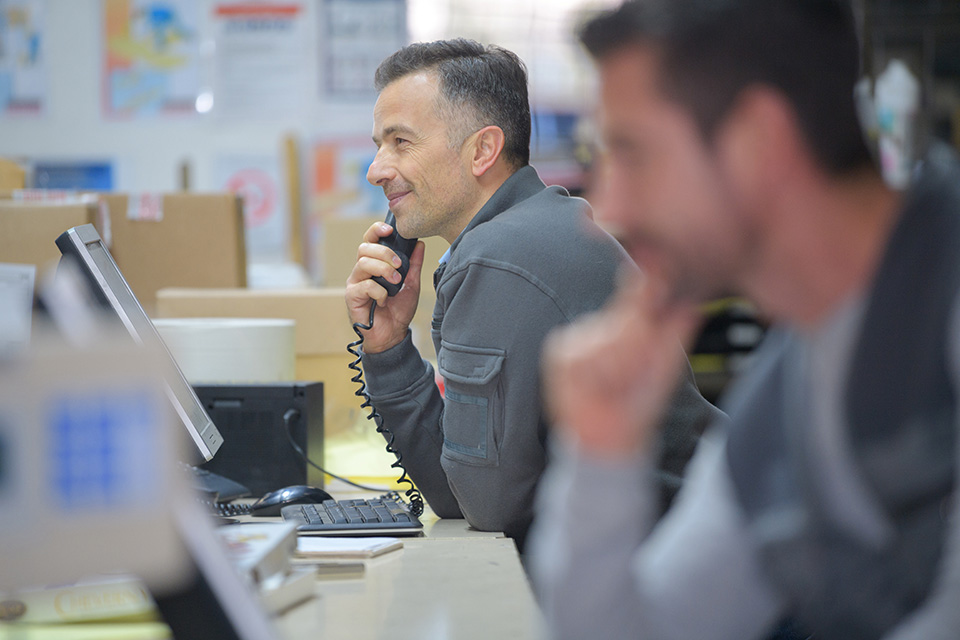
Our Approach
W.I.S. Logistics adds visibility and transparency to reverse logistics by using a cloud-based Transportation Management System (T.M.S.). This system allows each user throughout your organization to see only the details they want. It centralizes the data control and helps manage inbound freight costs to counter your outbound return costs.
Working with W.I.S. Logistics takes the mystery out of the reverse logistics process. We help make the unknown, known. Packaging, product quality, disposition, routing, and accounting codes are all accounted for in our approach.
"W.I.S. Logistics is great to work with - Corrie always gets me out of a bind! Everyone that I've spoken with at W.I.S. is always happy to assist, and their drivers are always on time. 100% recommend W.I.S. Logistics!"
-Amanda Miller, Logistics Supervisor, Schenck Process
Frequently Asked Questions
Reverse logistics is the process of managing the return of products from their final destination back to their point of origin, or to another designated location. Returns can occur because:
- Customer no longer needs the item
- Product reaches the end of its life cycle
- Product is damaged or flawed
- Items need to be disposed of or recycled
- Returns management
- Return policy & procedure
- Remanufacturing or refurbishment
- Packaging management
- Unsold products
- End-of-service life
- Delivery failure
- Rental equipment
- Repair and maintenance
- Establishing clear policies and procedures for returns
- Optimizing logistics networks to minimize costs and improve efficiency
- Leveraging technology or connections to improve visibility and accuracy
- Partnering with a logistics provider to streamline operations